Литейное производство. 1976. №11. С. 12.
Повышение эффективности вакуумирования стали в ковше
В.С. Сапиро, В.Т. Терещенко, М.М. Перистый, В.Я. Гагарин, С.В. Шлемко
Эффективность вакуумирования стали в ковше резко падает с увеличением его емкости до 3050 т из-за ферростатического давления, но его влияние
можно в значительной мере подавить при использовании высокой химической
активности твердого С, вводимого в металл в монолитном виде (рисунок).
Камерная установка для плавок до 10 т «Тулачермет» снабжена вакуумным пароэжекторным насосом НЭВ100х0.5 и имеет поворотную крышку 2, на которой смонтированы: дозатор для ввода раскислителей в ковш 3 под вакуумом в камере 1, механический пробоотборник металла и шлака и устройство для ввода в металл под вакуумом графитированного электрода 4 диаметром 200 мм.
Устройство представляет собой герметичный гидроцилиндр 6, на котором с помощью штанги и металлического ниппеля закреплен электрод (5 направляющая обойма).
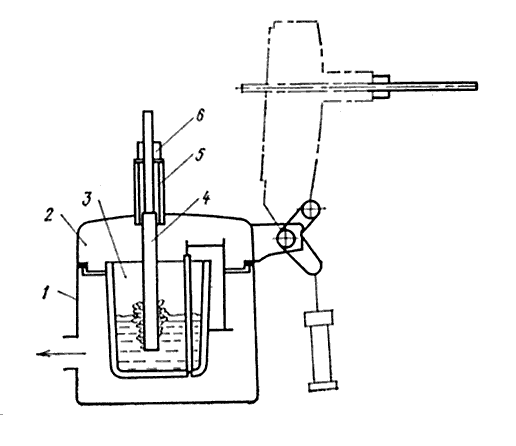
Вакуумной
обработке подвергали нераскисленные или раскисленные только Si стали с 0.040.80%С под окислительным печным или частично раскисленным
шлаком плавок 79 т. Монолитный углерод вводили в ковш после полного прекращения кипения металла, т.е. при достижении предельных результатов обычного вакуумировання (обычно через 2.53 мин после включения насосов
при 1530 мм рт. ст.; дальнейшее снижение давления до 13 мм рт. ст. уже не вызывало кипения). К моменту ввода графита в металле было 0.0020.006% O. Продолжительность обработки
монолитным С 1.52.5 мин, причем при вакуумировании нераскисленной стали через 11.5 мин после ввода стержня в ковш подавали дробленый ферросилиций ФС65.
Наблюдения
показали, что после ввода графита даже при 0.0020.003% О в стали возникало бурное кипение с полным уносом шлака в объем металла. Интенсивность
его была, как правило, выше, чем в первый период вакуумирования, а суммарный
выход продуктов раскисления (СОСО2) в 1.55раз, а в некоторых случаях в 57 раз больше (0.61.5 м/т против 0.180.93 м/т). Установлено, что интенсивность
кипения в процессе обработки стали графитом практически не зависит от
содержания кислорода в металле, а полностью определяется количеством шлака и
содержанием в нем окислов железа. Для обработки стали в 10-т ковше оптимальными условиями являются: 24% шлака при содержании в нем 810% Feобщ. Чрезмерно высокая окисленность шлака приводит к излишнему расходу графита, затягиванию процесса и неоправданным потерям тепла. Концентрация кислорода после обработки стали графитом снижалась с 0.00300.0063% до 0.00200.0025% или не изменялась, если этого уровня достигали уже после первого периода вакуумирования. В последнем случае эффективность процесса определялась дополнительным интенсивным барботажем металла и дополнительной его дегазацией. Усиления дегазации стали по Н не было замечено, так как уже при обычном вакуумировании металла в 10-т ковше концентрация Н составляет в среднем около 2 cм3/100 г. Влияние монолитного С как дегазатора стали под вакуумом хорошо прослеживается по поведению N, поскольку эффективность удаления его обычно низкая. Пробы металла на N отбирали по ходу вакуумирования и оценивали вклад каждого из периодов.
В первый период вакуумирования при средней начальной концентрации 0.0065 N эффективность его удаления составила 18.5%. Дополнительный барботаж во втором периоде позволил снизить концентрацию N еще на 17%. В целом эффективность удаления N при новом способе вакуумирования ~32%.
Обработка стали графитом под вакуумом сопровождается науглероживанием ее на 0.030.07%, что частично или полностью компенсирует обезуглероживание первого периода вакуумирования. В результате конечная концентрация С в стали
изменяется в пределах ±0.02% от исходной. Расход графитированных электродов
~0.81 кг/т может быть резко снижен, если обработку стали начинать еще в
период первичного вскипания, добиваясь лишь отсутствия выбросов металла из
ковша. В условиях литейных и электросталеплавильных цехов используют огарки
электродов.
© В.С. Сапиро, В.Т. Терещенко, М.М. Перистый, В.Я. Гагарин, С.В. Шлемко, 1976